Rapid Prototyping and 3D Printing: Revolutionizing Metal Fabrication
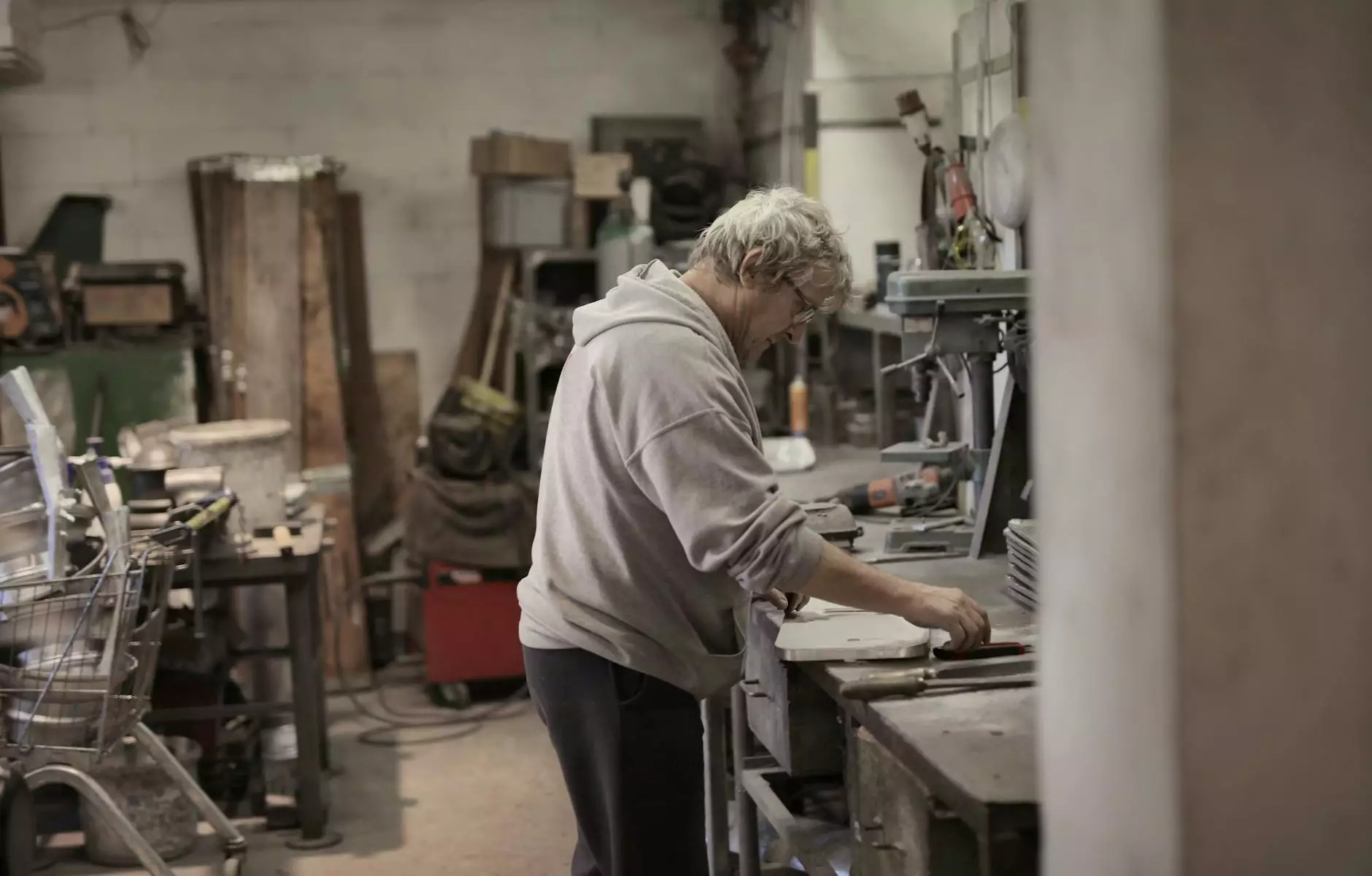
In the modern manufacturing landscape, the terms rapid prototyping and 3D printing have emerged as transformative forces, especially in the domain of metal fabrication. As companies seek to innovate and adapt to the ever-evolving market demands, understanding these technologies becomes imperative. This article delves deeply into the intricacies of rapid prototyping 3D printing, its advantages, and its profound impacts on the field of metal fabrication.
Understanding Rapid Prototyping 3D Printing
Rapid prototyping refers to a collection of techniques used to produce a scale model of a physical part or assembly using three-dimensional computer-aided design (CAD) data. The advent of 3D printing technology has enhanced this process, enabling manufacturers to create prototypes quickly and cost-effectively.
What is 3D Printing?
3D printing, also known as additive manufacturing, is a process of creating three-dimensional objects layer by layer. This technology stands in contrast to traditional subtractive manufacturing methods, which involve cutting away material to shape a product. The evolution of 3D printing has led to various applications across multiple industries, including healthcare, automotive, aerospace, and, notably, metal fabrication.
The Significance of Metal Fabrication
Metal fabrication involves the creation of metal structures by cutting, bending, and assembling processes. It's a critical component in various sectors, including construction, transportation, and machinery. As this field evolves, integrating advanced technologies like rapid prototyping 3D printing has become vital.
Advantages of Rapid Prototyping 3D Printing in Metal Fabrication
The incorporation of rapid prototyping through 3D printing in metal fabrication offers several advantages:
- Speed: 3D printing allows for faster prototyping compared to traditional methods. Manufacturers can develop and test designs swiftly, reducing time to market.
- Cost-effectiveness: By minimizing material waste and labor costs, companies can significantly reduce their production expenses.
- Design Flexibility: 3D printing enables intricate designs that may be impossible or prohibitively expensive to achieve with conventional techniques.
- Customization: Manufacturers can quickly adapt designs for specific customer needs, enhancing the product's market relevance.
- Complexity Simplified: The technology allows for complex geometries and lightweight structures, improving the overall performance of the final product.
How Rapid Prototyping and 3D Printing Work Together
In the realm of metal fabrication, rapid prototyping paired with 3D printing follows a systematic approach:
- Design: Engineers create a detailed 3D model using CAD software.
- Printing: The model is then converted into printable files, which guide the 3D printer in layering metal material.
- Post-Processing: Once printed, the prototype undergoes finishing processes, such as cleaning, heat treatment, or surface polishing.
- Testing: The prototype is evaluated for performance, allowing for necessary adjustments before final production.
Case Studies: Success Stories in Metal Fabrication
Numerous industries have successfully integrated rapid prototyping 3D printing into their metal fabrication processes. Here are some key examples:
Aerospace Industry
In the aerospace sector, companies are using 3D printing for lightweight components that reduce fuel consumption. For instance, using titanium alloys, manufacturers have produced complex parts that were traditionally too heavy or impractical.
Automotive Industry
Automakers leverage rapid prototyping to develop and test prototype parts efficiently. Customized parts can be fabricated rapidly, enabling faster iterations during the design phase. This flexibility leads to innovative vehicle designs and improved performance.
Medical Devices
In the medical field, 3D printing has enabled the production of bespoke surgical implants and prosthetics tailored to individual patients. This customization enhances patient outcomes and satisfaction.
Challenges in Implementing Rapid Prototyping 3D Printing
While the benefits of using rapid prototyping 3D printing in metal fabrication are significant, there are challenges to consider:
- Material Limitations: Not all materials are suitable for 3D printing, and sourcing the right material can be a challenge.
- Technology Costs: High-quality 3D printing machines can involve substantial upfront investments.
- Skill Gaps: A skilled workforce is essential to leverage these technologies effectively, and training may be required.
- Regulatory Compliance: In heavily regulated industries like aerospace and medical devices, meeting compliance standards can complicate the prototyping process.
The Future of Rapid Prototyping 3D Printing in Metal Fabrication
As technology continues to evolve, the future of rapid prototyping 3D printing in metal fabrication appears promising. Innovations in materials science, including the development of new alloys specifically designed for 3D printing, will expand the capabilities of manufacturing. Additionally, improvements in printing speeds and resolutions will further enhance the efficiency and quality of the prototypes produced.
Emerging Trends
Several trends are shaping the future of this industry:
- Increased Integration with AI: Artificial intelligence will play a critical role in optimizing designs and predicting failures, improving overall efficiency.
- Expansion of Materials: As research progresses, new materials, including composites and advanced alloys, will be developed specifically for 3D printing.
- Remote and Distributed Manufacturing: 3D printing allows for decentralized and on-demand production, reducing shipping times and costs.
- Sustainable Practices: The industry is moving towards eco-friendly materials and processes, integrating recycling into manufacturing pipelines.
Conclusion: Embracing the Future of Metal Fabrication
To remain competitive in an ever-evolving market, businesses must embrace the revolutionary capabilities of rapid prototyping and 3D printing. These technologies not only enhance metal fabrication processes but also set the stage for future advancements in manufacturing. Companies like DeepMould, operating within the metal fabrication sector, have the opportunity to lead the charge towards innovative practices that will define the landscape of the industry for years to come.
By adopting rapid prototyping 3D printing, organizations can not only streamline their operations but also cultivate a culture of innovation that is crucial for survival in the modern manufacturing environment.