Understanding the Role of a Hydraulic Tube Fittings Manufacturer
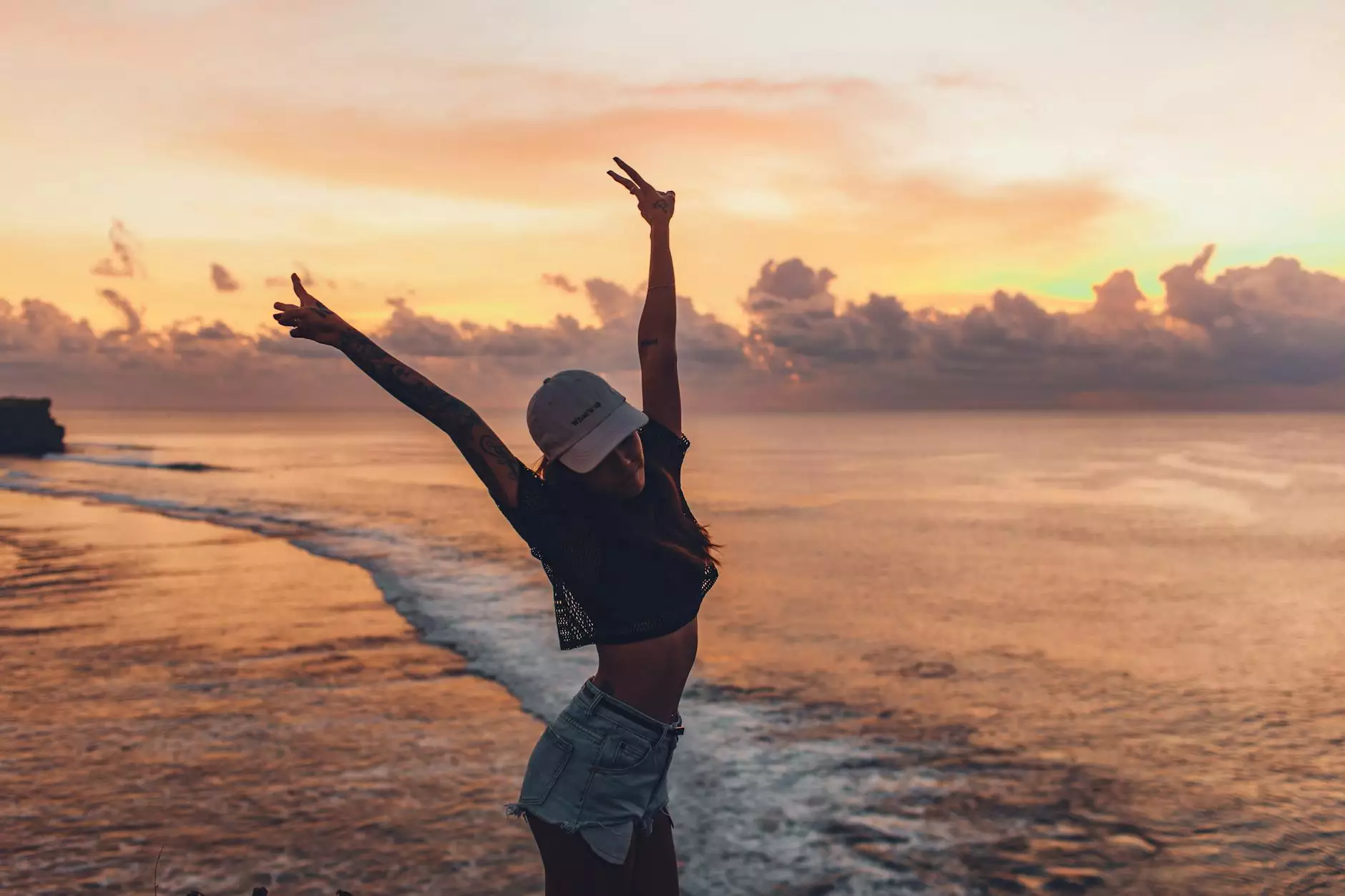
Hydraulic tube fittings are integral components in various industries, playing a crucial role in the functionality and safety of hydraulic systems. As a Hydraulic Tube Fittings Manufacturer, the responsibility lies in supplying high-quality products that meet rigorous standards. This article will delve into the intricacies of hydraulic fittings, the manufacturing process, and how organizations like Fitsch enhance operational efficiency and safety in hydraulic applications.
The Importance of Hydraulic Tube Fittings
Hydraulic tube fittings are essential for connecting hoses, pipes, and tubes within hydraulic systems. Their primary purpose is to maintain a strong, leak-proof connection while allowing for flexibility and movement. The importance of these components can be highlighted through the following points:
- Sealing Performance: High-quality fittings ensure minimal leakage under high pressure, which is crucial for system efficiency.
- Durability: Reliable fittings withstand the wear and tear of harsh operating environments.
- Compatibility: A wide range of fitting types allow them to be used in various hydraulic applications.
- Safety: Proper fittings minimize the risk of accidents and failures in hydraulic systems.
Our Manufacturing Process
At Fitsch, we understand that the quality of our products stems from a meticulous manufacturing process. Our dedication to excellence in the hydraulic tube fittings sector is evident in every step:
1. Material Selection
The foundation of any hydraulic fitting is the material used in its construction. At Fitsch, we prioritize premium materials such as:
- Stainless Steel: Known for its strength and resistance to corrosion.
- Brass: Offers excellent conductivity and resistance in certain applications.
- Carbon Steel: Provides durability and strength for high-pressure scenarios.
2. Precision Engineering
Each fitting is produced using advanced manufacturing technologies, including:
- CNC Machining: Ensures precision in every dimension, leading to high-quality connections.
- Hydraulic Pressing: Provides robust formation under controlled conditions.
- Surface Finishing: Enhances corrosion resistance and aesthetic appeal.
3. Quality Assurance
No product leaves our production floor without undergoing rigorous quality checks. Our testing protocols encompass:
- Leak Testing: Ensures every fitting can handle operational pressures.
- Dimensional Inspection: Confirms adherence to specifications.
- Material Testing: Verifies the integrity and performance characteristics of the materials used.
Types of Hydraulic Tube Fittings
The diversity of hydraulic systems necessitates an array of fitting types. Here is an overview of various hydraulic tube fittings supplied by Fitsch:
1. Compression Fittings
Compression fittings are widely used for connecting tubing in hydraulic systems. Their design allows for easy installation while providing a tight seal without the need for additional sealing materials.
2. Threaded Fittings
These fittings utilize a threaded connection to create a secure joint. They can be used in various applications, thanks to their versatile design.
3. Flange Fittings
Flanged fittings provide a strong connection points, often used in high-pressure systems or applications requiring frequent disassembly.
4. Quick Connect Couplings
Quick connect couplings allow for rapid connection and disconnection of hoses, ideal for applications where frequent changes are necessary.
Innovative Solutions for Industry Applications
With the growing demand for innovation, Fitsch aims to provide tailored solutions for different sectors, including:
- Construction: Supplies fittings capable of withstanding harsh construction site conditions.
- Manufacturing: Offers specialized fittings to meet production line requirements.
- Aerospace: Develops fittings that meet stringent industry regulations for safety and performance.
- Automotive: Provides robust solutions for hydraulic systems in vehicles.
Choosing the Right Hydraulic Tube Fittings Manufacturer
When selecting a Hydraulic Tube Fittings Manufacturer, consider the following criteria:
- Experience: A manufacturer with years of expertise is more likely to deliver quality products.
- Certifications: Look for manufacturers with ISO certifications indicating adherence to international quality standards.
- Customer Service: Responsive support can significantly enhance your purchasing experience.
- Product Range: A wide selection of fittings and custom solutions can cater to diverse needs.
Commitment to Sustainability
At Fitsch, our responsibility extends beyond simply manufacturing fittings. We are committed to sustainable practices, including:
- Eco-friendly Materials: Sourcing materials that have a lower environmental impact.
- Energy-efficient Processes: Implementing manufacturing practices that minimize energy consumption.
- Reduced Waste: Strategies that aim to reduce scrap materials and promote recycling.
Final Thoughts
Choosing the right Hydraulic Tube Fittings Manufacturer can significantly impact the efficiency, safety, and reliability of your hydraulic systems. With a commitment to quality, innovation, and sustainability, Fitsch stands out in the market. By investing in our high-quality fittings, industries can ensure that their hydraulic systems operate at optimal levels. For more information on our products and services, visit Fitsch today.
Hydraulic Tube Fittings Manufacturer